The 9-Second Trick For Sheroz Earthworks
The 9-Second Trick For Sheroz Earthworks
Blog Article
Our Sheroz Earthworks Statements
Table of ContentsThe Definitive Guide to Sheroz EarthworksFacts About Sheroz Earthworks UncoveredSheroz Earthworks Can Be Fun For AnyoneSheroz Earthworks Fundamentals ExplainedNot known Details About Sheroz Earthworks
When service providers like Rasch Construction implement a grade control system for their dozers, it helps them make less blunders when rating. This system continually checks the blade, makes little modifications to the setting of the dozer blade during grading and reduces rework. If the dozer does not quality the ground precisely as prepared, the operator can straighten the dozer blade to deal with small errors and make exact changes to reach the wanted quality.When thinking about the purchase of a grade control system for a dozer, drivers will certainly need training on how to make use of the system. New drivers and experienced veterans should recognize with the parts of the 3D quality control system, including the equipment (for example, the sensors and receivers) and the software program elements.
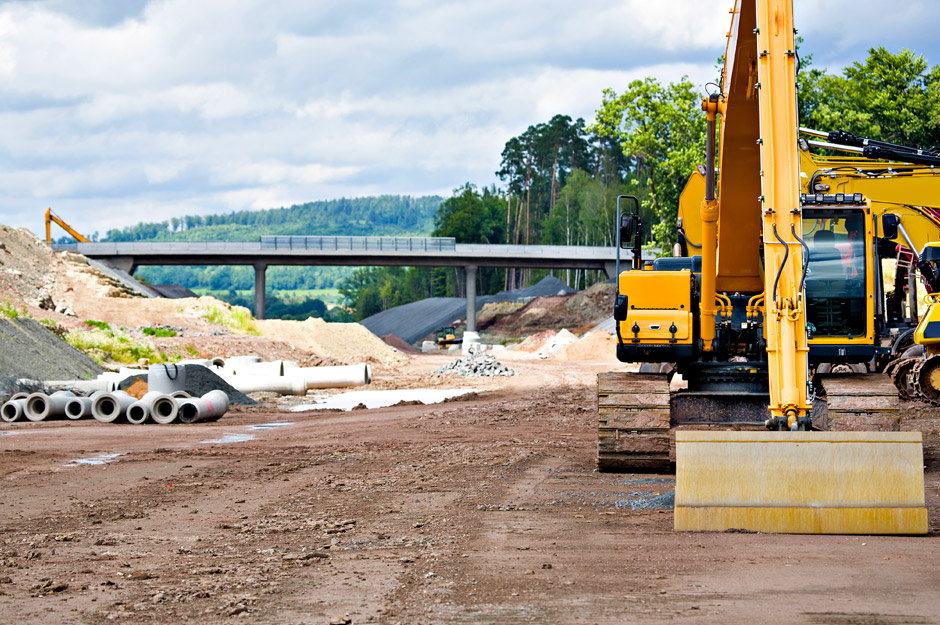
What Does Sheroz Earthworks Mean?
This consists of quality info, altitude data and various other relevant metrics presented on the LCD screen inside the dozer's taxi. Last, driver training ought to consist of how to properly control the dozer blade making use of the 3D grade control system. This assists them recognize how the system readjusts the blade in response to grade variants.
Product savings: If the grade is extra precise, a specialist might require much less product for the jobsite. Operators may also lower the requirement for rework and boost cost savings due to labor and products - https://peatix.com/user/22107431/view. To get more information regarding exactly how to improve jobsite performance with grade control technology, discover the offerings from Trimble and similar firms
Assistance and precision control, the base components of modern equipment control for building, have actually remained to evolve given that broad productization started in the mid-1990s. However, the worth proposal has actually become also sweeter since, with worth being realized beyond the roi (ROI) of the general service providers and the overall task cost for the customers.
The Sheroz Earthworks PDFs
The roots of device control stretch back a century. The Historical Building Devices Organization (HCEA) presumes that the A.W. French & Co. "energy grader" of the 1920s, a crawler-mounted system that utilized stringline control, may be the extremely first example and this before electronics and computer. Nonetheless, it was the advent pop over here of real-time kinematics (RTK) for GPS in the mid-1990s that brought maker control as we recognize it to the building and construction website, and together to precision agriculture.
After that it relocated to accuracy control, such as blade control, and later propagated to even more courses of motorized equipment, improved with more sensing unit combination. The effect on building and agriculture has actually been indisputable: productivity gains, much less rework, a lot more efficient handling of products, shorter timelines, site security renovations, and much more - https://www.easel.ly/browserEasel/14473256. These benefits are as noticeable to customers and operators as they were in the early days of adoption, gains from nearly three decades of development
Automation is not nearly rate; it is also around better control of the load and stress on the equipment and moving just the right amount of materials so as not to position a burden on it. (Image: CHCNAV) These 2 tasks, as each of our talked to specialists testify, stand for the lion's share of recognized efficiency gains.
Sheroz Earthworks Things To Know Before You Get This
"Besides the skid steer systems, there are more excavators made than all the various other devices types incorporated," stated Daniel Sass, product supervisor of device control at Hemisphere GNSS. "Excavators are the workhorse. And people utilize them differently, and they make use of other pieces of devices to enhance excavators somewhat in a different way.
Certainly, by volume it is excavators and compact excavators." Numbers aid inform the story. "In the USA, a minimum of in a three-year duration from 2019 to 2022, concerning 253,000 excavators were offered, for which I have quite reputable data, but just 61,000 dozers and just 7,000 scrapers," Sass said
If you most likely to Europe, where they utilize excavators for lots of other jobs, the symmetrical effect may be greater." Operators can conveniently assess the ROI of going digital for specific items of devices such as excavators, but component of the reward could be that basic service providers are needing subcontractors to be geared up and all set to fit right into a more full electronic site.
"A great deal of larger sites. "Just how do you move the material? With operator support, Clark claimed, it is not uncommon to see efficiency gains of 30% to 40%, also with inexperienced operators.
6 Easy Facts About Sheroz Earthworks Described
There are substantial gains to be made in operator support for less complicated hefty devices, such as compactors. "Usually a contactor will certainly put a less experienced operator in the compactor," Clark said. "In manual days, to get rid of the capacity of under-compaction and missing out on areas, they would certainly develop fairly a large overlap, possibly approximately 40% of overlap in between courses.
Report this page